Our Group Home has moved. Please visit our Group Website for other Business Lines and Country Sites.
Factors Influencing Cast Iron Prices: A Comprehensive Guide
Explore the factors influencing cast iron prices per Kilogram (KG) and per Metric Ton (MT). Learn how material grade, weight, complexity, machining, and market dynamics shape costs, and discover tools to estimate precise pricing. Perfect for buyers and manufacturers alike!
CASTING PRACTICES
12/2/20242 min read
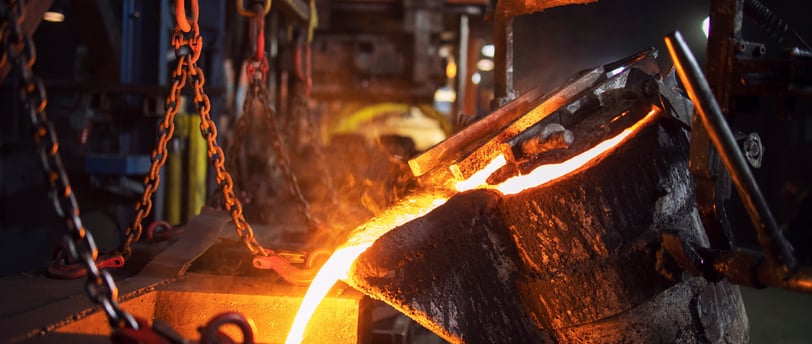
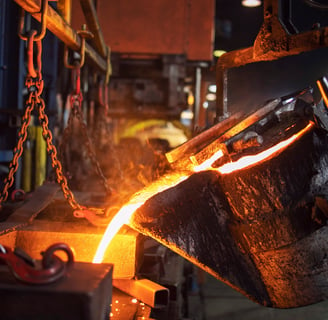
The price of cast iron castings, whether calculated per kilogram (KG) or per Metric Ton (MT), is determined by a range of critical factors. For manufacturers and buyers, understanding these elements is vital to optimizing costs and ensuring value for money. Here's an in-depth look at the primary influences on cast iron pricing:
1. Material Composition and Grade
The type of cast iron used directly impacts its cost. Higher grades, such as ductile iron, come with enhanced properties like durability and tensile strength but may require more expensive raw materials and processing techniques. These qualities often justify their higher price.
2. Casting Weight
The weight of a casting has a dual impact on pricing:
Heavier Castings: These require more raw material, leading to increased costs.
Lightweight Castings: While consuming less material, smaller castings (e.g., under 1 kg) often involve higher precision and labor input, which can elevate costs.
Balancing size and production requirements is crucial for accurate cost assessment.
3. Design Complexity
Simple designs are cost-effective, but intricate castings demand advanced techniques like multi-part molds or additional sand cores. This complexity increases labor, material, and time investments, raising the overall price.
4. Casting Process Selection
The production method chosen has a significant influence:
Shell Molding: Preferred for complex or high-tolerance castings but tends to be more expensive.
Green Sand Casting: Cost-effective for less intricate designs or larger production volumes.
Selecting the optimal method based on the design and production scale is key to cost efficiency.
5. Machining Requirements
Post-casting processes, such as machining, play a significant role in pricing. Components requiring precise machining—especially using CNC equipment—are more expensive. Streamlining machining needs can help reduce costs without compromising quality.
6. Quantity Ordered
The order size often determines economies of scale:
Small Orders: Higher costs per unit due to setup and production inefficiencies.
Large Orders: Bulk production reduces per-unit costs and often qualifies for supplier discounts.
Planning order quantities strategically can yield considerable savings.
7. Market Dynamics
Global market conditions, including the availability of raw materials, energy costs, and labor rates, directly affect cast iron pricing. Staying updated on these trends can help buyers anticipate fluctuations and plan purchases more effectively.
A Solution for Accurate Estimation
For those seeking pricing, our Cast Iron Price Estimator provides valuable insights. By inputting specific parameters such as material, weight, and machining needs, users can estimate the cost for their cast iron castings with ease.
Conclusion
The cost of cast iron castings is influenced by a combination of technical and market-driven factors. By understanding the interplay of material grade, casting weight, design complexity, process selection, machining needs, order size, and market conditions, manufacturers and buyers can make informed decisions. Whether your focus is on small components or large-scale production, knowing these cost drivers is the first step to achieving efficiency and profitability.
For additional information on how Exxelmet castings can benefit your specific application, get in touch with us here on send an email to contact@exxelmet.com.
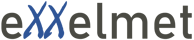
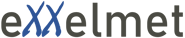
Copyright © 2025 Exxelmet
P-200, Benares Road, P. O. Netajigarh, Howrah, West Bengal, India. Pin Code 711108
Tel: +91 98311 11541
Email: contact@exxelmet.com