Our Group Home has moved. Please visit our Group Website for other Business Lines and Country Sites.
How Cast Iron Castings Are Made: Detailed Step-by-Step Process
Cast iron castings are renowned for their strength, durability, and versatility across industries. Understanding how these castings are made reveals the precision and expertise required in their production. Here, we take you through a comprehensive step-by-step process to explain how cast iron is made and why Exxelmet is the leading manufacturer of cast iron products. #CastIronCounterweights #EnergyEfficiency #Sustainablility #Manufacturing #CastIron #CustomCounterweights #ElevatorCounterweight #Engineering
CASTING PRACTICES
Rupesh Madhogaria
12/18/20243 min read
Step 1: Sourcing High-Quality Raw Materials
The process begins with sourcing the raw materials. Cast iron is primarily made from pig iron, scrap iron, and steel, combined with alloys such as carbon and silicon. Typically, the composition includes:
Pig Iron: 70-80%
Scrap Iron and Steel: 10-20%
Alloys (Carbon and Silicon): 2-5%
These materials are carefully inspected for quality to ensure the final product meets rigorous standards.
Step 2: Melting in the Furnace
The raw materials are melted in a high-capacity furnace at temperatures exceeding 1,150°C (2,100°F). The types of furnaces commonly used include:
Cupola Furnace: Traditional and cost-effective, often used for large-scale production.
Electric Induction Furnace: Highly efficient and environmentally friendly, suitable for precise control of metal composition.
Rotary Furnace: Versatile and used for specialized applications requiring uniform heating.
During this process, the materials are mixed to create a uniform molten iron blend. The chemistry of the molten metal is meticulously monitored to maintain precise composition.
Step 3: Molding
Once the molten iron is ready, it is poured into molds made from sand, resin, or metal. The molds are designed based on the desired shape and size of the casting. This step is crucial for ensuring that the final product matches the required specifications.
Step 4: Cooling and Solidification
The molten iron in the molds is allowed to cool and solidify. This cooling process ensures that the casting takes its final shape while maintaining structural integrity. Proper cooling prevents defects and ensures the casting's durability.
Step 5: Cleaning and Finishing
After solidification, the castings are removed from the molds and cleaned. This includes removing excess sand, scale, and other impurities. Additional finishing processes, such as grinding, machining, and polishing, are performed to achieve the desired surface quality and dimensions.
Step 6: Material Grades and Quality Inspection
Cast iron is available in various grades, each suited for specific applications. Common material grades include:
Gray Iron: Known for its excellent machinability and thermal conductivity.
Ductile Iron: Offers superior strength and flexibility.
White Iron: Highly resistant to abrasion, ideal for wear-resistant applications.
Malleable Iron: Combines strength and ductility, used in industrial fittings.
Every cast iron casting undergoes rigorous quality inspections. These include dimensional checks, material tests, and performance evaluations to ensure the product meets industry standards and customer requirements.
Step 7: Packaging and Delivery
The final step involves securely packaging the castings to protect them during transportation. Our logistics team ensures timely delivery to clients, maintaining our reputation as a reliable partner in cast iron manufacturing.
Industrial Applications of Cast Iron
Industrial cast iron is utilized across various sectors due to its exceptional properties:
Automotive Industry: Engine blocks, brake drums, and components.
Construction: Pipes, manhole covers, and structural elements.
Agriculture: Tractor parts, plowshares, and machinery.
Cookware: Durable pans, pots, and griddles.
Energy Sector: Wind turbine hubs and generators.
Manufacturing: Machine bases, tools, and industrial equipment.
Benefits of Using Cast Iron
Cast iron offers several advantages, making it a preferred choice across various industries:
Durability: Cast iron products have exceptional strength and resistance to wear and tear.
Heat Retention: Ideal for cookware and industrial applications, cast iron retains heat efficiently.
Versatility: Used in automotive, construction, and kitchenware industries, among others.
Cost-Effectiveness: Cast iron provides a long-lasting solution at an affordable cost.
Why Choose Exxelmet your Leading Manufacturer of Cast Iron
As a global leader in the production of cast iron castings, Exxelmet bring decades of expertise, cutting-edge technology, and an unwavering commitment to quality. Our manufacturing facilities are equipped with state-of-the-art machinery, ensuring precision and efficiency at every step.
Key Differentiators:
Custom Solutions: We provide tailor-made cast iron products to meet your specific needs.
Sustainability: Our production process incorporates eco-friendly practices, reducing waste and emissions.
Global Reach: With a robust supply chain, we deliver cast iron products to clients worldwide.
Customer Support: Our dedicated team ensures seamless communication and support, from order placement to delivery.
When you think of "what is cast iron" or "how cast iron is made," think of Exxelmet - your trusted partner for all cast iron needs.
Contact us today to learn more about our premium cast iron castings and experience the benefits of working with the industry's best.
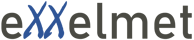
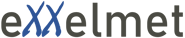
Copyright © 2025 Exxelmet
P-200, Benares Road, P. O. Netajigarh, Howrah, West Bengal, India. Pin Code 711108
Tel: +91 98311 11541
Email: contact@exxelmet.com